Edwards Air Force Base Main Runway Reconstruction - Antelope Valley, CA
Project Focus
Edwards Air Force Base, located in the Mojave Desert approximately 100 miles north of Los Angeles, serves a unique and critical function. It is the premier military flight test facility in the world and the command center for proving and improving the critical national defense systems of the past, present and future.
The 15,000’ long by 300’ wide main concrete runway at Edwards is the central hub for testing missions at the base and provides the takeoff runway for the Boeing 747 “piggy-back” space shuttle return to Cape Canaveral.
IHC combined its expertise in the construction of complex heavy-duty airfield pavements with the innovative design and project management skills of CH2M HILL to form a joint venture (JV) for the design and construction of these critical facilities. The USACE short-listed the JV during the SOQ solicitation and subsequently awarded the team the $94 million Design-Build contract based on two-phase “Best Value” selection criteria. Originally built in 1952, the existing PCC runway was showing significant distress due to Alkali Silica Reaction (ASR), threatening safe operations and the success of the base testing mission. Prior to decommissioning the main runway, the JV was required to design and build a full-service “temporary” 12,000’ long by 200’ wide runway in the infield between the main runway and the North Base parking aprons, allowing base operations to continue without interruption while the main runway was reconstructed in the summer of 2008. The USACE awarded the project in mid-2006 and the JV began design immediately on a fast-track basis for the temporary runway.. Construction began in mid-summer 2007 and opened to flight operations on May 19, 2008 – a contract milestone necessary begin the removal and replacement of the main runway with PCCP. Upon successful completion of the Main Runway, the opening ceremonies for the facility took place on October 31, 2008, two months ahead of schedule and on budget.
Project Details
Schedule & Complexity Constructing this project at the world’s second largest air force base, the home of the Air Force Flight Test Center and 95th Air Base Wing, presented several logistical and operational challenges. The base has 19 runways—three are paved and the other 16 are located on the lakebed. Edwards is also a landing site for the NASA Space Shuttle and hosts more than 100,000 visitors annually.
Key accomplishments for this project include:
- Trained more than 1,500 workers through the project’s safety program resulting in the team logging more than 400,000 hours without a lost-time accident
- Built two runways in less then two years
- Moved 44,000 truck loads of rock, sand and asphalt and more than 800,000 cubic yards of earthwork
- Placed 28 miles of concrete
- Demolished 445,000 square yards of concrete in 9 weeks
Construction & Innovation The CH2M HILL design team prepared five separate construction packages to facilitate the implementation of the project. By ‘fast-tracking’ the design and working closely with the ‘build’ element of the team, the schedule for design approvals was controlled to meet the complex phasing for the project while maintaining critical base operations. The team worked to efficiently develop construction plans and specifications that met the DOD requirements without unnecessary duplication of drawings or details.
The design team used the Pavement-Transportation Computer Assisted Structural Engineering software program (PCASE) to optimize the pavement design section to meet all functional requirements while utilizing the best combination of locally available aggregates and construction methodology.
The JV did substantial due diligence during the first year to “prove” the quality of aggregate in a local gravel pit that had previously been unused for concrete coarse aggregate. The JV ran numerous mix designs to optimize the mixes for slipform constructability in the severe desert environment. In this manner, the JV was able to reduce the thickness of the main runway while still exceeding the strength requirements used in verifying the structural design.
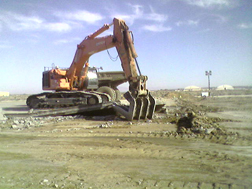 |
The JV constructed the temporary runway with asphalt pavement on crushed aggregate base and the three intersections where the temporary runway meet the taxiways that connect it to the main runway with PCCP concrete on rigid base. CH2M HILL-IHC constructed significant apron work, including two new Arm/De-arm pads and two new Power Check pads, along with the temporary runway.
The reconstruction of the Main Runway, entailed the complete removal of the existing runway. It took two backhoes working in tandem loading dump trucks and hauling the waste concrete to an onsite disposal area to complete this effort. The design requirements for treatment of unsuitable and unstable base materials required significant subgrade preparation of the underlying base materials prior to placing the PCCP. The JV then placed the PCCP for the Main Runway reconstruction on a rigid base course produced from blending discarded materials from the PCC coarse aggregate production at the aggregate pit. Concrete was central-mixed on-site and hauled to the grade in double end dump trailers. A CMI 550 paver was used to slipform the concrete to 12”, 16” and 20” depths while meeting the strict edge and elevation tolerances.
The main base runway reconstruction maintained full operational capabilities by relocating the BAK-12 (barrier arresting kit) from each end of the existing main base runway to the temporary runway. Upon completion of the main runway reconstruction, the JV moved the BAK-12s back to the main runway.
Quality Control The JV implemented comprehensive project quality control plans for design and construction to meet the exacting standards of the Corp project specifications. Testing and inspection of all key processes ensured compliance and top quality. The JV ran numerous mix designs using several local sources to optimize the mixes for slipform constructability in the severe desert environment and to provide a reliable 90-day concrete flexural strength compatible with PCASE design thickness.
IHC used a combination of several techniques ensure quality, including two high-production water chilling units with additional tank storage. Equipment and plant preparation began prior to daylight enabling placement to begin at dawn. Special misting systems were placed on the paver and curing machine to provide a favorable atmosphere above the slab allowing for all paving to take place during the day, in an extremely hot, dry, and windy environment. Stockpiles were sprinkled with water to facilitate additional evaporative cooling, and specialty admixtures were used to control initial set time. This attention to detail contributed to the outstanding quality of the surface and edge tolerance – not a single plastic shrinkage crack developed, a noteworthy achievement under such harsh conditions.
Safety
  |
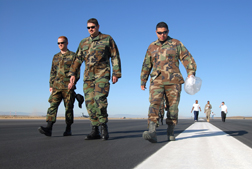 |
   |
Military personnel perform a FOD walk to ensure the runway is clear of debris before use. |
   |
Safety is paramount at this very busy air base; thus daily coordination is detailed and well planned to accommodate flight plans, stand downs, and coexistence with base operations. The JV implemented strict processes for control of Foreign Object Debris (FOD) in all air operations crossings to ensure no damage to aircraft from the debris created by the thousands of truck movements required to deliver aggregates and remove existing pavements.
Partnering for Success Edwards is a major USAF training and test flight facility and the back up landing strip for the Space Shuttle; therefore, the construction activities required for the Main Base Runway reconstruction could not compromise its mission-ready capabilities. Before any work began, the CH2M HILL-IHC JV Team committed to use a collaborative partnering process to work with the USACE, USAF, Base Engineering, Subcontractors, Vendors and all other stakeholders, to openly discuss issues, possible solutions, and resolve points of conflict to prevent negative impacts on the base operations and maximize design-build efficiency. The JV held formal partnering sessions at key milestones from the award of the contract throughout the entire course of the project. Each meeting served a specific, timely purpose. They identified the principles that all project participants would operate within; reviewed and established design goals; established protocols for mobilizing and startup; identified how the inclusive JV, USACE, and the USAF team would remove the “rocks in the road” discovered while construction was underway;
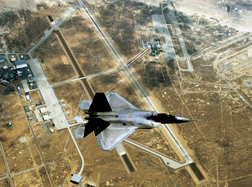 |
created high-performance "Tiger Teams" to establish protocols for transferring operations and managing schedule recovery; as well as many other steps to ensure timely delivery of a project of the highest quality.
IHC credits the entire project team for completing the design and construction of the project in a collaborative and partnering environment that engaged all stakeholders to the benefit of the project.
|