DIA International Runway 34/16
Project Focus
The opening of Runway 16R-34L and associated taxiways was an important economic milestone for Denver and the Rocky Mountain West. The 16,000’ by 200’ "International" runway, 33% longer and 33% wider than the other jumbo runways, was designed to accommodate the next generation of large commercial aircraft. More importantly, it allows for year-round, trans-oceanic, direct service from Denver to Asia and Europe. The additional length affords fully loaded and fueled departing aircraft the necessary ground speed required for lift-off in the hot "thin" air summer months.
Project Details
Schedule & Complexity The Contractor improved the contract schedule by six weeks, opening the project in just two years on September 4, 2003. This was a huge challenge primarily because of the sheer size of the project and the short construction seasons in Denver. The project scope included 890,000 sy of 12" lime-treated subgrade and cement-treated base, 30 miles of edge drain, 865,000 sy of 17" and 21" PCCP, 75 miles of electrical conduit servicing 4,000 airfield lights and signs, 350 manholes and 450,000 tons asphalt and asphalt permeable base. Difficulties facing vendor partners were project deadlines in production and delivery of 1.2 million tons of aggregate and 150,000 tons of portland cement and fly ash.
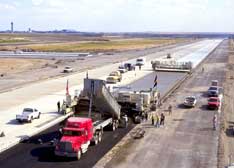 |
The Contractor received notice to proceed in mid August 2001 but early progress was limited as the grading contract was not yet complete, FAA funds flow became questionable, winter was approaching and new requirements for security were implemented immediately after 9/11. The project team went to work, establishing a realistic schedule compatible with different funding scenarios, and incorporating the required 11 milestones, 9 construction restrictions and 2 full winter seasons. The construction team completed approximately 85% of the PCCP by Fall 2002. Finally a Spring 2003 snowstorm dropped from 36" to 60" of fresh wet snow on Denver which helped alleviate a 3-year drought but was not a welcome event for construction progress. Stakeholder team effort and innovative problem solving throughout the project resulted in the runway opening ahead of schedule.
Construction & Innovation All paving materials were produced on-site. An Excel pug mill turned out up to 7,200 tons per day of cement-treated base; two 12 cy Rex central-mix plants produced up to 9,000 cy of concrete per day for multiple combinations of simultaneous PCCP placement operations; and a portable asphalt plant produced 4,000 tons per day for shoulder base and pavement. GPS machine controls and hand-held units placed and trimmed the 8" cement treated base course and grade checked. The Contractor used six different slipform paving machines and two form-riding finishers, including Gunter Zimmerman models 1500 and 850 and CMI models 450 and 350; a Bidwell drum finisher; and Clary rolling screed to maintain schedule and productivity.
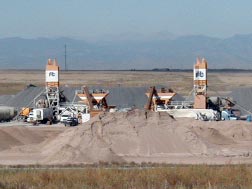 |
The project team worked with airport operations to combine work areas for tie-ins to the existing runway and taxiway system, reducing the time required for closure by 60 days on the taxiway tie-ins. The team worked up to the safety zone limits in normal daytime activities, completely eliminating the need for the 90 projected nighttime runway closures.
Quality The Contractor, with special care in all construction slipform processes, met a strict FAA "true" 0.04-foot elevation while maintaining a 90-degree vertical face on longitudinal construction joints. The final profilograph smoothness averaged 3.0 inches per mile on the runway and 4.0 on the taxiway. A final check resulted in the removal of only one panel out of 23,000 - less than 0.01%. The results of the Contractor QC process controls proved extremely successful in production of an outstandingly uniform, quality concrete. The project average standard deviation was 26.1 psi with an average mean strength of 733.8 psi - a feat even more noteworthy in that it was accomplished using two concrete plants.
|